Current turnaround time is 8 weeks
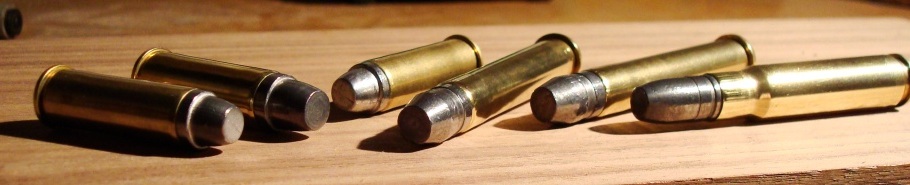
Frequently Asked Questions
We answer a lot of questions on this page. Please take some time to see if your question is answered here before ordering or reaching out to us for information.
What's the price and what's the wait time?
Wait time is always posted in the upper right corner of the home page. Prices can be found under "Prices & Ordering" in the navigation bar.
What about handles?
My molds accept Lee six cavity handles. RCBS handles also fit, except some newer RCBS handles have reduced diameter screw holes, in somewhat erratic locations. Minor modification to the RCBS handle may be required. I do not make or sell handles.
What is meant by "Body diameter" on the order form?
It's the major diameter, which is usually the driving bands. Many designs don't have driving bands so I use the term "body".
For unusual, multi-diameter designs, use "Special notes" to CLEARLY describe the critical dimensions and locations of critical diameters, including the tolerance window. Orders without included diameter tolerance cannot be filled.
What body diameter should I order? What's the best fit for my barrel?
I can't say. It's your chamber, and you have to do the research or measure it. That is entirely your responsibility.
I'll be sizing to .432". What diameter should I order?
Ordering .432" with the (default) positive tolerance window will give full contact with your sizing die. There's no need to order even larger, but you can if you want to.
I want an "as cast" diameter as close as I can get to .3215".
I have a diameter tolerance window of .002" for my molds.
When ordering a diameter such as .432", you can select:
- Positive tolerance (+.002/-.000) means the diameter will be AT LEAST .432"
- Negative tolerance (+.000/-.002) means the diameter will be AT MOST .432"
- Centered tolerance (+/- .001) means as close as possible to .432"
Positive tolerance is usually desirable for driving bands.
Negative tolerance is usually best for bore ride noses or any application where a certain diameter cannot be exceeded and a sizing die won't be used on that portion of the bullet.
Centered tolerance might be desirable when powder coating, and tapered designs.
Using "Special Notes" on the online order form, you can refine your diameter request for bore ride, body diameter, whatever, to the 4th decimal place. Ordering to the half thousandth does not ensure precision to the half thousandth, it only helps you communicate the desired diameter range within that .002" window.
My mold cavities are actually turned to +/-.0001" tolerance, but I cannot guarantee resultant casting tolerance closer than .002" because of casting variables such as pour technique and temperature, mold block temperature, purity of alloy, etc.
When specifying the diameter I want, can I request an undersized front band? For example, .360"?
Yes. It's common practice to use cast bullets that are .002" or more oversized, but often the chamber's throat is not that large, preventing chambering if any part of the bullet north of the crimp groove is greater than nominal diameter. In a situation like this example, "body diameter" could be selected as .360" (+.002/-.000) plus tolerance for sizing, and the front driving band diameter specified as .358" (+.000, -.002) negative tolerance to ensure that the band is not over .358", since it will not engage a sizing die if one is used.
This detail can be requested using "Special Notes" when ordering.
This is not often required, but can be applied to any applicable design when needed. If in doubt, you've gotta measure.
Do you discount for multiple, identical molds?
Yes. The discount will be shown in your shopping cart.
What are some of the properties of the different mold metals?
2024 Aluminum is very durable, light weight, and inexpensive. Its propensity to change temperature quickly is seen by some as a disadvantage, since molds produce their best bullets within a narrow temperature sweet spot.
Ductile Iron is the most durable of the commonly used mold metals. It is easier to maintain a more consistent temperature. It is lighter weight than brass and heavier than aluminum. Its biggest disadvantage is propensity to rust. Iron is rough on delicate boring tools, and so it is the most expensive.
360 Brass is a bit heavier than iron, and costs less because of ease of machining. It maintains temperature very well. Some see its weight as a disadvantage.
Sprue plates and hardware are carbon steel.
My favorite for my own casting is aluminum.
I see two block size choices for a multi-cavity mold. Why?
Extra large blocks are handy for big, heavy bullets. Having more metal, they maintain better temperature stability.
What is the 1.8" XXL Aluminum, listed in the mold block choices?
Extra thick to allow up to .940" diameter. Also extra tall at 1.73" to accommodate outsourced hollow point conversion of long designs.
Why does the order form require that I select a casting alloy?
In order to produce the requested bullet diameter, I need to know how much tin is in the alloy. All applicable alloys shrink as they solidify. The more tin, the less shrinkage. The alloy choices in the drop down menu are listed in order of expected shrinkage, from greatest to least. If you intend to use varied alloys, choose the most appropriate one that's highest on the list, so that other alloys with more tin will be a bit larger.
Do I want the sprue plate trough?
Good fill out requires a generous sprue puddle. The mold must be held level to avoid spilling over the side. The trough increases the amount of liquid alloy held confined on the plate.
Good castings require that each cavity be completely and quickly filled, one at a time. The trough makes this more difficult because of liquid alloy prematurely spilling into the next cavity. Both types of plate require a few minutes of practice to master. After that, either type works fine.
Some people really prefer the trough. Most people do not like it.
Can you cut different designs within the same block?
Yes, each additional design adds $20 to the price of the mold.
Will you supply mold block blanks without cavities?
Mold blanks for Magma and Ballisti-Cast casting machines can be added to your cart from our products page, "Prices & Ordering".
For hand casting mold blanks, please email us.
I see designs in your catalog marked "Basis for hollow base nose pour"?
I don't do hollow base, or nose pour. But I can cut the cavity completely through the mold block from the bottom. The mold block is shortened to approximately 1.375" length to accommodate this. After you receive the mold you will need to finish it by making and installing the base pin which seals the bottom and creates the hollow.
To hire this work done, contact Erik at www.hollowpointmold.com.
Do you make hollow point molds?
No.
Can you make round ball molds?
No.
Can I have a sprew plate with pour holes that are larger, smaller, or different bevel?
No.
Can you go smaller than .30 caliber?
Just barely. The bullet cannot be smaller than .270" at the grooves, so 7mm designs can have only very shallow lube grooves if any. A 6.5mm could have no grooves at all. No gas checks under 30 caliber.
What's the best bullet design for my double barreled 8.3 x 79mm Napstick Needlehammer?
The best bullet is always the one that fits the best. You must take the appropriate measurements.
Can we talk on the phone?
Short answer is maybe, while in the shop we probably won't hear the phone ring and we aren't going to answer the phone outside of normal working hours. If we hear the phone ring we will pick up. The best way to reach us is e-mail, and it's far more effective since we can send you proposed design drawings and you can send photos and such.
I want a design that's not in your catalog. How do I get a custom?
Refer to "Submitting a new design" on the home page.
How do I maintain the mold properly?
The interface between mold block and sprue plate should be kept clean and lubed. Graphite works well, and synthetic 2-stroke oil is also popular. Keep the surfaces clean to prevent galling. Lead smear can easily be removed while casting, using a small rag while the mold is hot.
Gas check notes:
Hornady 45 caliber GCs measure .460" outside diameter (OSD), with a bell mouth of about .461". They are intended for use with both rifle and handgun. If you are going to size your rifle bullets to .460" or larger they will probably not crimp on. The rifle sized Gator gas check is recommended. It takes the same shank size but is extra thick for a larger OSD.
Gator checks (Bullet Swaging Supply Inc.) are now available for the 9.3mm. 375 cal. checks have traditionally been used in the past, and the Gator uses the same shank size but is thinner for a more appropriate OSD of .371".
40 - 41 caliber gas checks:
The Hornady 416 GC is .392" ISD. Gator also offers this size. Don't be put off by the name; this gas check is for the 41. Like their 45 caliber it is intended for both rifle and handgun. Sizing down the extra .006" is just as easy as it is for the 45.
.391" is my default shank size for the 41.
The old Lyman style 41 cal. GC is .397" ISD. It is only .007" thick and like all of the original Lymans does NOT crimp on. Gator checks of this type (G410P1) are available to keep the old Lyman molds running, but even Lyman has abandoned this old design. A shank that's small enough to allow installation will also allow them to fall off. I can provide this shank size if requested, but I advise against it.
Gator checks (type G410P2, or 41BSS) are also available, with dimensions of .414" OSD (.417" at the bell mouth), .380" ISD. These work well for the 10mm/40 caliber, and are my default shank size for those bullets. You can request this odd shank size on your 41 caliber mold if desired.
There is a new Gator check, the 40BSS which can also be used on the 10mm/40. This requires a .367" shank which I can do upon request.
Unless requested otherwise, my 40 caliber GC molds will have .379" shanks for the 41BSS gas check.